Oversight on Local Sourcing of Personal Protective Equipment
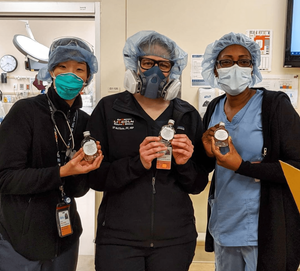
Good morning. I am Adam Friedman, Director of the Pratt Center for Community Development. I appreciate the opportunity to testify about some of the opportunities we see arising out of the local production of PPE, but also to sound a note of caution.
Pratt Center runs the Made in NYC program which includes more than 1,400 local manufacturers. Made in NYC quickly became a center for information about emergency assistance for manufacturers, how to produce PPE and how to get into the emerging supply chains. Three big takeaways:
First, the City organized new supply chains for masks and gowns and other PPE around the existence of manufacturing clusters. Two of these clusters were in Manhattan's Garment Center which was recently rezoned to encourage office development, and another cluster in Sunset Park, which was being rezoned at that time. Given the vulnerability of those areas to displacement, I truly fear that if the pandemic had struck even just two years later, the city would not have had the essential capacity to produce sufficient PPE because so many companies would have been displaced.
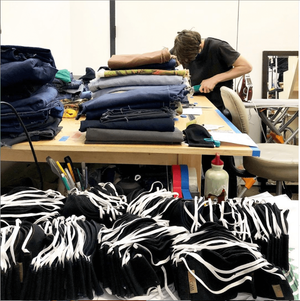
The issue raised is not just about PPE, but about how much production capacity—an economic development and a safety issue—a city of 9 million people needs to maintain the functionality and safety of the city. This is true of everything from food to auto repair and is a really compelling argument for both more comprehensive planning and including this information in environmental statements when it rezones.
Second, the City proved it can act quickly and boldly if it needs to, such as it did to find PPE. So, the purchase of PPE can be an instrument of economic development for smaller, BIPOC and Women-owned businesses. We heard from many smaller companies that they were not selected to be included in these supply chains, mostly because they were too small. But the city now has the opportunity to plan ahead. The city, and the state, need to find the political will to reach these smaller and MWBE firms.
Last, the garment industry which is the most likely supplier of much of the PPE, is very cyclical: it has slow months and it has busy months. This seasonality is bad for the workers at risk of being laid off. The city should explore how to use the purchase of PPE as a counter-cyclical measure to stabilize some piece of the industry and improve job quality.
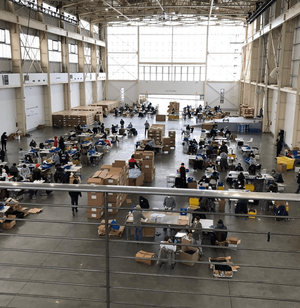